Cost Analysis for Building a 16 x 20 Deck
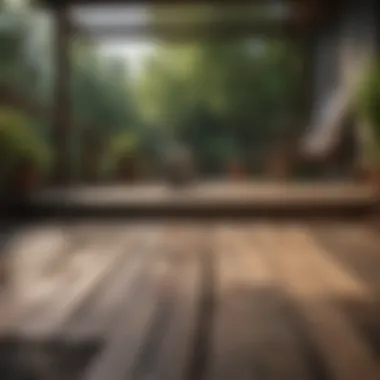
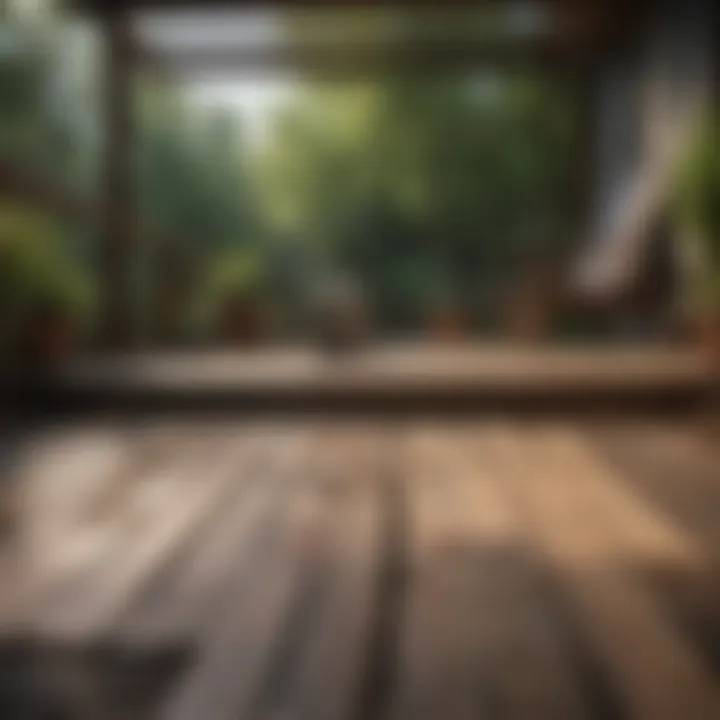
Intro
Building a deck is a significant investment for any homeowner. Specifically, a 16 x 20 deck enhances outdoor space, offering a perfect spot for gatherings, relaxation, or simply enjoying nature. However, understanding the associated costs is crucial for making informed decisions. From material choices to labor expenses, various factors can influence total expenses. This article provides an in-depth exploration of these elements, emphasizing the importance of careful planning and budgeting. Homeowners, design enthusiasts, and anyone considering a deck will find valuable insights here.
Design Inspiration
Trending Styles
When constructing a deck, it's important to consider current trends that can elevate its aesthetic appeal. Popular designs vary from modern minimalist styles to rustic charm. Open designs with ample space for furniture allow for versatile usage, while multi-level decks can create dynamic visual interest. Some homeowners opt for integrated seating or built-in planters, which add functionality and enhance the outdoor experience. The choice of design should not only resonate with personal taste but also harmonize with the overall style of the home.
Color Palettes
The color of the decking can significantly affect the overall appearance. Natural wood tones like cedar or redwood offer a warm, organic feel. Conversely, composite materials come in various colors, allowing for unique palettes. Choosing a darker shade can contribute to a contemporary look, while lighter colors can create a feeling of brightness and openness. When selecting colors, consider how they will interact with the surrounding landscape and the home’s exterior.
Practical Tips
Maintenance & Care
Maintaining a deck is vital for its longevity and functionality. Regular cleaning prevents the buildup of dirt and debris, which can lead to rot or mold growth. Applying a sealant every few years is essential for protecting wood materials from moisture and UV damage. Composite materials require less upkeep but still benefit from occasional washing to maintain their color and appearance.
Budgeting & Planning
Before beginning construction, developing a thorough budget is necessary. Expenses may vary based on material selections, size, and labor costs, depending on regional pricing strategies. Here’s a breakdown of key budget components:
- Materials: Wood, composite, railings, and finishes.
- Labor: Professional installation vs. DIY.
- Permitting: Local regulations may require permits, adding to costs.
- Finishing touches: Furniture, lighting, and landscaping to complete the space.
Careful consideration in these areas will support financial planning and ultimately lead to a successful deck installation.
Prelims to Deck Construction Costs
Building a deck can be an important addition to any home. Knowing the construction costs is crucial for homeowners who are thinking about this investment. This section discusses what influences these costs and their implications.
Understanding the Basics of Deck Dimensions
When talking about decks, size matters. A 16 x 20 deck means there are 320 square feet of area where you can relax and entertain. This size is often chosen because it is not too small for gatherings and not too large to overwhelm a yard. Understanding the dimensions provides a baseline for estimating materials and labor needed for construction. The larger the deck, the more it will cost due to increased material usage.
Importance of Deck Size in Cost Assessment
The size of the deck fundamentally affects the overall budget. As previously mentioned, a bigger deck requires more materials, which directly affects the costs. Here are key points to consider:
- Material Costs: More square footage directly leads to increased material costs. This includes decking, framing, and railing.
- Labor Costs: Relying on professionals means more time on the job site, thereby increasing labor fees.
- Permits: Some areas require permits based on the size of the deck, which can add to the total expenses.
Factors Influencing Deck Construction Costs
When planning to build a deck, understanding the various factors that influence construction costs is essential. Costs can vary significantly based on several criteria. A thorough examination of these factors allows homeowners to make informed choices, optimizing their investment.
Material Selection: Wood vs. Composite
The choice of material is a major factor in cost assessment. Traditional wood decks, often made from pressure-treated lumber, tend to have lower initial costs. However, they require ongoing maintenance, such as staining and sealing, which can increase long-term expenses.
On the other hand, composite materials like Trex offer a more durable, low-maintenance option at a higher upfront cost. They do not splinter, rot, or insect damage, making them a good choice for longevity. It is important to weigh the initial investment against future costs. Choosing between these options impacts not only financial aspects but also aesthetic preferences.
Design Complexity and Custom Features
Adding design complexity can significantly influence total costs. Simple, basic designs will be more affordable than intricate layouts with custom features such as built-in seating, multi-level decks, or specialized railings. Custom features contribute to aesthetics and functionality but also increase the labor and material costs. Homeowners should carefully consider the balance between their vision for the deck and budget constraints.
Regional Cost Variations
Another important consideration is the geographical location of the project. Construction costs fluctuate depending on regional economic conditions, demand for materials, and labor availability. For instance, urban areas often experience higher price tags than rural settings due to labor costs and transportation fees. It is beneficial for homeowners to conduct local market research. Understanding regional price trends can help in setting a realistic budget and avoiding surprises during the construction process.
Material Costs Breakdown
Understanding the material costs associated with deck construction is crucial for homeowners. This section provides an overview of the various materials available, their associated costs, and why these factors matter in the overall budget for a 16 x 20 deck. Materials not only dictate the initial expense but also influence maintenance costs and lifespan.
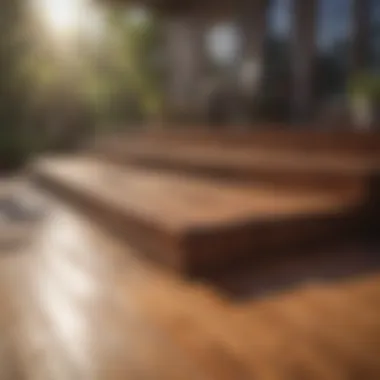
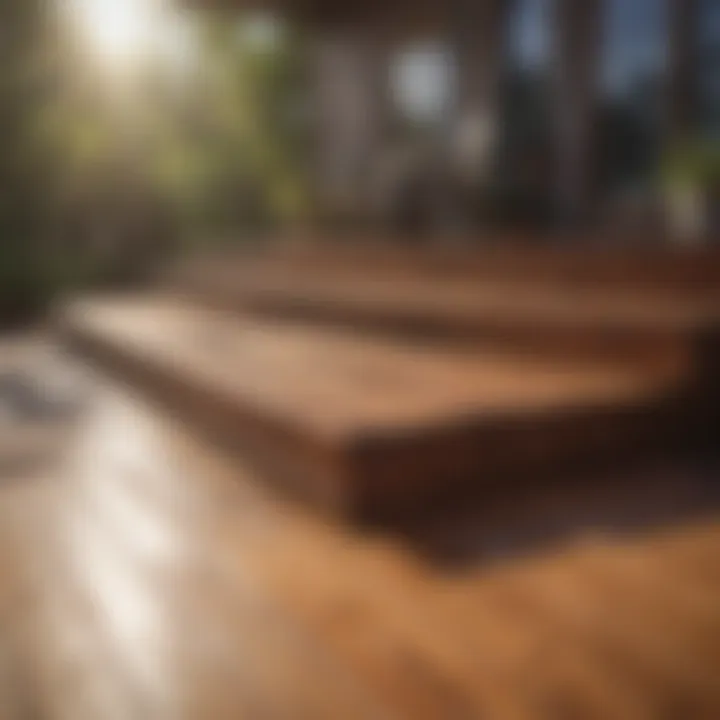
When choosing materials, consider factors such as aesthetics, durability, and the level of maintenance required. These choices will directly impact how much you will spend overall and how long your deck will last.
Wood Decking Options and Their Prices
Wood decking remains one of the most popular choices for many homeowners. It offers a classic look and practicality. There are several kinds of wood you may consider for your deck. Each comes with different price points and characteristics.
- Pressure-Treated Lumber: This is the most economical option. It can cost around $2 to $5 per square foot. This wood needs regular maintenance, including sealing and staining.
- Cedar Wood: Known for its natural beauty and resistance to decay, cedar typically costs about $4 to $8 per square foot. Although it is more expensive than pressure-treated wood, its aesthetic appeal can increase property value.
- Redwood: Offering outstanding durability and a rich color, redwood can be around $6 to $12 per square foot. However, like cedar, it also requires periodic maintenance to keep its appearance.
- Hardwoods: Exotic woods such as Ipe or Teak can cost between $8 to $15 per square foot. They are very durable and beautiful but require more investment and care.
Choosing wood requires balancing cost against your preferences for maintenance and durability.
Composite Decking: A Cost Evaluation
Composite materials have grown in popularity in recent years due to their low maintenance needs and longevity. These materials are typically made from a combination of recycled wood fibers and plastic. The cost for composite decking usually ranges from $5 to $15 per square foot, depending on the brand and quality.
Some well-known brands such as Trex and TimberTech provide options with varying price points.
Benefits of Composite Decking:
- Low Maintenance: Unlike wood, composite decks do not require regular staining or sealing, which can save money in the long run.
- Durability: Resists fading and warping, making it suitable for various climates.
- Sustainability: Many composites use recycled materials, making them an environmentally friendly choice.
It is also worth noting that composite decking can simulate the appearance of natural wood without the associated maintenance. This offers an appealing option for many homeowners looking to avoid frequent upkeep.
Other Material Considerations
While wood and composite materials are the most common choices for decks, there are other options worth considering based on specific needs and aesthetic preferences.
- Aluminum: Known for its extreme durability, aluminum decking can resist corrosion and warping. Prices generally range from $10 to $15 per square foot. It's particularly useful in wet climates.
- Vinyl: Vinyl decking is made from PVC and offers excellent durability and low maintenance. Costs can fall between $4 to $10 per square foot.
When evaluating these materials, also keep in mind the cost of railings and accessories like lighting. These elements can significantly impact the total costs. Planning according to your envisioned deck's style can help set a more accurate budget.
"Choosing the right materials can dramatically affect your deck’s lifecycle and maintenance needs. Consider life-cycle costs, not just initial expenses."
Your choice of materials plays a pivotal role in shaping the overall experience of owning a deck. Be sure to weigh initial costs against long-term needs and advantages.
Labor Costs Involved in Deck Construction
When it comes to building a deck, the labor costs can often be a significant part of the overall expense. Understanding these costs is essential for homeowners who wish to create a budget that accurately reflects the financial commitment involved. Labor costs not only include the hiring of professionals but also the potential savings from a do-it-yourself approach. Evaluating these aspects can lead to a clearer picture of the total cost of constructing your deck.
Hiring a Professional vs. DIY
The decision between hiring a professional contractor and tackling the project on your own is often pivotal. Hiring a professional can ensure that the deck is built to code, with proper installation of materials and safety precautions in place. Professionals bring experience and expertise, which can result in a more durable and aesthetically pleasing structure. This may save you money in the long run by avoiding costly mistakes.
On the other hand, choosing a do-it-yourself route can significantly lower labor costs. If you have the required skills and tools, DIY allows for greater control over both the design and the process. However, it is crucial to have an honest assessment of your capabilities.
- Professionals:
- DIY:
- Typically charge hourly or a flat rate
- Provide warranties for their work
- Have access to better resources and materials
- Requires personal investment of time and effort
- Risk of errors that could lead to additional expenses
- Potential to learn valuable skills
Estimating Labor Hours Needed
Estimating the number of labor hours required for deck construction can be a complex task. Several factors influence this estimate, including the size of the deck, chosen materials, and design complexity. A straightforward 16 x 20 deck might take anywhere from 30 to 80 hours of labor depending on experience and resource availability.
To better understand the time commitment, consider these aspects:
- Preparation Time: This includes designing, gathering materials, and obtaining necessary permits. In some cases, this time can equal or exceed actual construction time.
- Site Preparation: Clearing the area and leveling the ground takes considerable time and often requires specialized equipment.
- Building the Frame: The primary structure needs to be sturdy, requiring precise measurements and cuts.
- Installing Decking Boards: Depending on the type of material, this can be a time-consuming process.
Tip: Make sure to add additional buffer time for unexpected issues. It is common for projects to take longer than initially planned.
Accurate estimation of labor hours requires a careful evaluation of each phase of building. Keep in mind that more complex designs will naturally lead to increased time and cost.
Calculating Total Costs for a x Deck
Calculating the total costs associated with constructing a 16 x 20 deck is vital for homeowners and enthusiasts who wish to make informed financial decisions. This section provides clarity on essential factors influencing overall expenses, which ensures budget alignment with home improvement projects. Understanding these costs can aid in avoiding unexpected financial burdens later on. Moreover, it facilitates effective planning, enabling homeowners to prioritize their spending on materials and labor according to their needs and preferences.
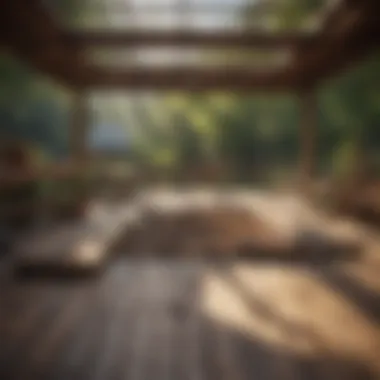
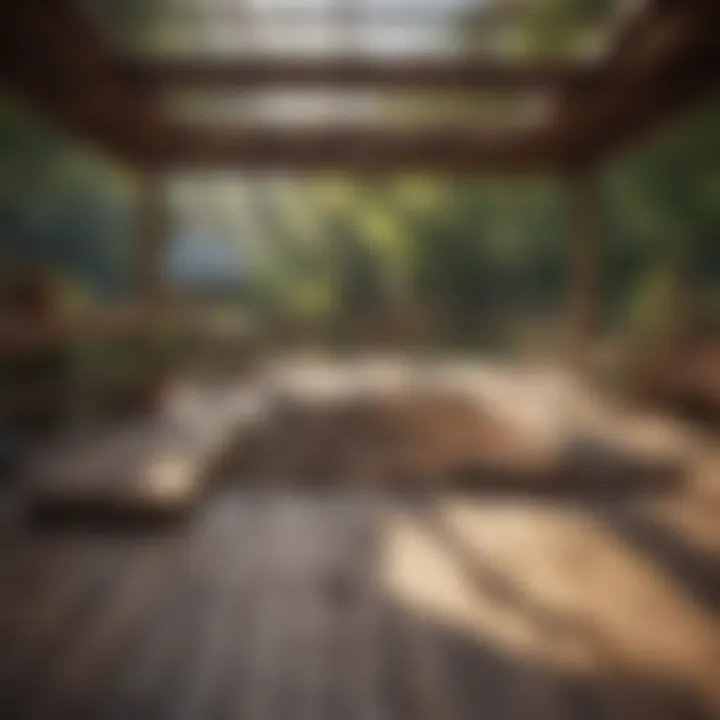
Estimating Material Costs
Material costs play a crucial role in the overall budget for deck construction. The type of material chosen significantly affects both the initial investment and long-term maintenance expenses. Common options for decking materials include treated lumber, cedar, and composite materials. Each type has its own price range and benefits.
- Treated Lumber: Generally the most affordable choice, with prices around $2 to $5 per square foot. However, it may require regular maintenance to upkeep its appearance and prolong its lifespan.
- Cedar: Offers natural beauty and resistance to decay. Prices range from $3 to $7 per square foot. Yet, it also necessitates maintenance, such as staining and sealing, to protect against weathering.
- Composite Decking: While initially more expensive, with costs from $5 to $12 per square foot, it is low-maintenance and more durable over time.
Additionally, the presence of features like railings, stairs, or built-in seating will impact material costs. Each added feature requires specific materials, which will further adjust the overall budget.
Estimating Labor Costs
Labor costs can significantly influence the total expenditure of building a deck. The decision to hire professionals or undertake a DIY project should be made thoughtfully. Professional contractors often charge between $15 and $35 per hour, depending on their experience and your geographic location. The complexity of the design is another key factor affecting labor time. A basic rectangular deck will require less labor compared to a multi-level structure with intricate designs.
If considering a DIY approach, homeowners must still account for their time invested. Underestimating the hours required for construction can lead to project delays and unanticipated costs, especially if additional help is needed.
A rough estimation indicates that a 16 x 20 deck may take around 40 to 60 hours of labor, depending on the chosen material and design. Ensure to include time for preparation, actual building, and cleanup.
Final Cost Estimation Example
To illustrate how to calculate total costs, let’s consider a sample budget for constructing a 16 x 20 deck using treated lumber.
- Material Costs: 320 square feet (16 x 20) at an average of $3 per square foot:
- Labor Costs: Assuming 50 hours at a professional rate of $20 per hour:
- Total Cost:
This estimation serves as a guide, noting that individual choices and regional pricing may vary. Consider potential additional expenses, like permits or inspections, which have not been included here. Moreover, it’s beneficial to seek multiple quotes to ensure you receive competitive pricing for both materials and labor.
Return on Investment for Deck Construction
The financial implications of building a deck extend beyond the initial construction costs. Homeowners often seek to understand the return on investment (ROI) for such projects. This examination is crucial in determining whether the investment in a 16 x 20 deck adds tangible value to a home. Factors like the material used, market trends, and the deck’s design play significant roles in calculating ROI.
Analyzing the ROI not only informs homeowners of potential future gains but also shapes their choices during the construction process. Homeowners should weigh the long-term benefits against the outline costs to make decisions that align with their financial goals.
Market Trends in Home Value Appreciation
Understanding the current market conditions is essential when assessing ROI for deck construction. Recent data indicate that homes with well-constructed outdoor decks can see an increase in value. According to various real estate studies, properties equipped with quality outdoor spaces typically appreciate faster than those without. This appreciation can significantly impact resale value.
Home buyers often seek properties that offer outdoor entertainment space. A deck serves as a versatile area for gatherings, relaxation, or simply enjoying the outdoors. This demand can lead to a higher selling price, increasing the overall ROI when it comes time to sell.
A few points compiled from different market analyses include:
- The average ROI for a deck generally hovers around 70-80%.
- Composite decks usually provide a better ROI than wooden decks due to their longevity and low maintenance features.
- Regions with warmer climates might experience higher demand and ROI for decks due to year-round usability.
Factors Affecting ROI
Several elements can influence the return on investment for a constructed deck. Recognizing these factors allows homeowners to maximize their potential gains:
- Quality of Materials: High-quality materials generally lead to a better ROI. For example, composite decking may cost more upfront but yields less maintenance and longer lifespan, improving overall value.
- Design and Layout: A well-planned deck that complements the architecture of the home can enhance aesthetic appeal, attracting more buyers and elevating home value.
- Local Real Estate Trends: The home market varies widely by location. Homes in desirable neighborhoods with greater demand for outdoor spaces tend to see a higher ROI.
- Permits and Compliance: Ensuring the deck is built according to local regulations can prevent setbacks that diminish ROI. Homeowners should obtain necessary permits and follow local building codes to avoid complications during a sale.
By understanding these factors, homeowners can make informed choices about their deck construction project. Investing time and resources into a well-planned outdoor space is a strategic move that often results in satisfactory returns.
Case Studies: Real Costs from Homeowners
Understanding the real costs associated with constructing a 16 x 20 deck is invaluable. Case studies from actual homeowners provide a lens into the nuances of deck construction that might not be immediately apparent through theoretical analysis alone. These personal accounts encompass various elements such as material choices, labor practices, and geographical influences, offering a multi-faceted view of the financial considerations at play.
Homeowner experiences reveal not just the hard numbers but also the emotional and practical aspects of the construction process. For potential builders, these insights are crucial in shaping expectations and informing decision-making when it comes to budgeting and design choices.
Homeowner Experiences and Their Costs
In reviewing various homeowner experiences, a range of costs emerge, reflecting different choices and circumstances. One homeowner in Ohio described their project involving pressure-treated pine, finding materials and labor brought the total cost to approximately $4,500. Meanwhile, a family in California chose composite decking and reported a price of around $8,000 after installation. Variations stem from regional pricing, material costs, and availability.
Homeowners have shared diverse experiences:
- Material Choices: Some prioritized aesthetics and opted for premium hardwood, resulting in higher costs but a visually striking deck.
- DIY vs. Professional Help: Individuals who hired contractors observed costs nearly 30% higher than those who employed a DIY approach, emphasizing the influence of labor on total expense.
- Unexpected Expenses: Common additional costs included permits, hidden repairs beneath existing structures, or design adjustments during the build.
Lessons Learned and Recommendations
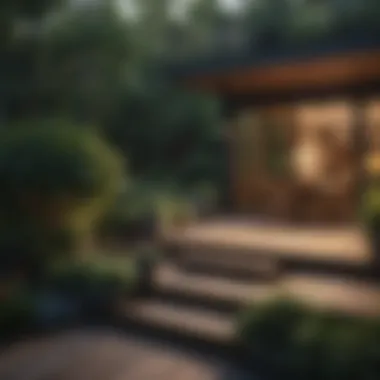
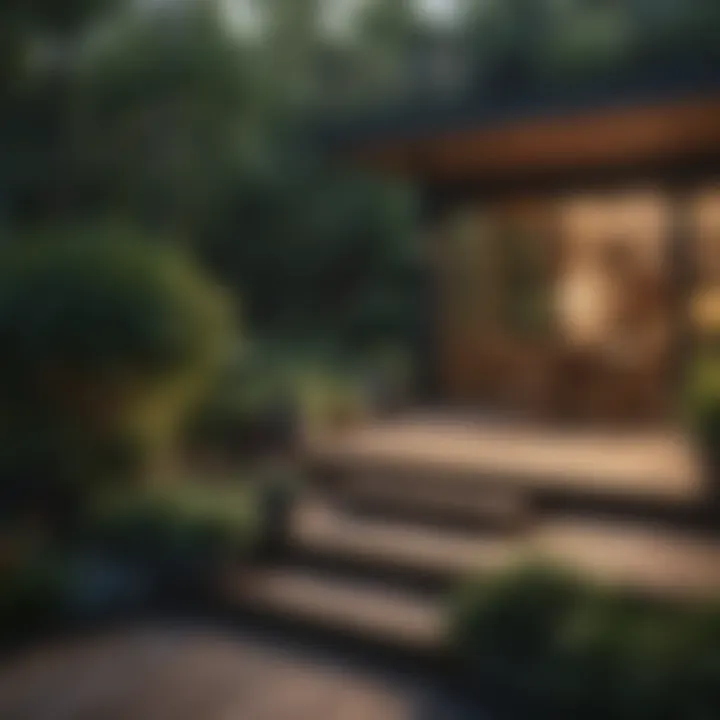
Documented lessons from these case studies offer valuable insights. Homeowners often suggest to carefully budget for unexpected costs, ideally adding 10-20% to the original estimate. Many recommend involving a contractor early on for accurate assessments. This helps in avoiding decision fatigue and spurs timely completion of the project.
Some specific recommendations include:
- Research Materials: Understand the long-term implications of material choices, including maintenance and durability.
- Consult Local Regulations: Be informed about local building codes and permits from the outset to prevent delays.
- Plan for Accessories: Consider additional costs for features such as railings, stairs, or staining, which can significantly affect the overall budget.
The insights gathered from these real-life examples empower future homeowners to navigate the complexities of deck construction with greater confidence, emphasizing that well-informed decisions significantly impact budget outcomes.
Permits and Regulations Impacting Costs
Building a deck might seem like a straightforward project, but there are various permits and regulations that can significantly influence the overall cost of construction. Understanding these elements is crucial for homeowners who wish to ensure compliance with local laws while managing their budgets effectively. This section of the article examines local building codes and the costs associated with acquiring necessary permits.
Understanding Local Building Codes
Local building codes are set by municipal or regional authorities and serve as guidelines that dictate the construction standards that must be met during a project. These codes may vary widely between different areas, reflecting local climate conditions, community standards, and safety requirements. Compliance with building codes is not optional; failure to adhere can result in fines or the need to redo parts of the project to meet regulations.
Homeowners should be aware of several specific elements related to building codes that can impact costs:
- Foundation and Structural Requirements: Local codes may dictate specific materials and construction techniques to ensure structural integrity. For instance, in areas prone to severe weather, multiple footings may be needed, which can increase labor and material expenses.
- Safety Regulations: Building codes often include safety features like railing heights and stair dimensions. Homeowners must ensure these features are included in their plans, which may affect the design and, consequently, costs.
- Zoning Laws: Zoning laws can restrict the size and location of your deck on your property. If the proposed project does not comply, additional costs may incur in terms of redesigning or applying for special permits.
By understanding local building codes, homeowners can avoid unexpected delays and costs, optimizing their construction efficiency.
Costs Associated with Permitting
Permitting is the process of obtaining the necessary approvals from local authorities before starting a construction project. Each city or county has its own permitting requirements, which can vary in terms of complexity and cost. Here are some essential considerations related to permitting costs:
- Application Fees: Most local jurisdictions charge an application fee for processing the permit request. Fees can vary based on the scope of the project, the materials used, and the local government’s policies.
- Inspection Fees: A permit often requires several inspections during construction to ensure compliance with building codes. Each inspection may involve additional fees, contributing to the overall cost.
- Plan Review Fees: If your project requires a detailed review by a city planner, there may be an associated fee. This review assesses whether the proposed construction meets local regulations and standards, adding potential costs to your project.
All these fees and requirements can add up quickly. Homeowners should factor in these permitting costs when budgeting for their deck construction and plan accordingly to avoid unexpected expenses.
"Understanding your local building codes and permit costs can save you significant money. It helps in planning and reduces risks during the construction phase."
Maintenance Considerations and Ongoing Costs
When deciding on constructing a 16 x 20 deck, one must consider maintenance as a crucial element of the overall cost evaluation. The initial outlay for materials and labor is only part of the equation. Long-term care and ongoing expenses can add significantly to the total investment. This section examines the various aspects of maintenance and their associated costs, including how these factors can impact the deck’s longevity and aesthetics.
Expected Maintenance Costs Over Time
Expected maintenance costs for a deck can vary considerably based on materials used and local climates. Typically, maintaining a wood deck can incur more costs over time compared to composite materials. Homeowners should plan for regular inspections, cleaning, and possible repairs.
- Cleaning: Routine cleaning might involve power washing, which can cost anywhere from $100 to $300 annually if done by professionals. If you opt for DIY cleaning, the purchase of cleaners, brushes, and other tools should be considered.
- Sealing and Staining: Wood decks usually require sealing every one to three years. This process can cost between $200 and $800 depending on the size and condition of the deck. Composite materials generally require less frequent treatment, though they also benefit from occasional cleaning.
- Repairs: Over time, expected wear and tear on the deck may lead to repairs, especially for wood. If boards splinter or rot, replacing them could cost between $20 to $50 per board.
Long-Term Durability of Materials
Understanding the durability of the materials chosen for the deck is vital. The long-term cost of maintenance is linked directly to the material’s resilience.
- Wood Decking: Pressure-treated wood, cedar, and redwood are common choices. While they are more cost-effective initially, wood can degrade due to weather, insects, and regular use. It generally lasts around 10 to 20 years with proper maintenance.
- Composite Decking: Made from a blend of wood fibers and recycled plastic, composite decking offers improved durability and resistance against rot, splintering, and insect damage. These decks can last 25 to 30 years or more, requiring less frequent maintenance, which can offset the higher initial cost.
"Investing in more durable materials might increase the upfront cost but could reduce ongoing maintenance significantly."
Considering maintenance from the start can save homeowners both time and money in the long run. It's essential to factor these elements into your overall budgeting plan to ensure a satisfactory experience with your 16 x 20 deck.
Culmination
Understanding the conclusion is vital in this article. It summarizes key points discussed throughout the piece. A well-structured conclusion not only reinforces important findings but also provides clarity on the overall topic. In this case, it emphasizes the complex factors contributing to the costs of constructing a 16 x 20 deck.
Summarizing Key Cost Factors
When evaluating the cost of a deck, several aspects can impact the final budget. Key factors include:
- Material Choices: The type of material selected will make a significant difference in cost. Wood and composite materials vary greatly, affecting both initial expenses and long-term maintenance.
- Labor Expenses: Hiring professionals versus taking a DIY approach has financial implications. Professional labor costs tend to be higher but could save time and guarantee quality.
- Design Features: Custom designs and added features can enhance the visual appeal but may inflate overall costs.
- Regional Pricing Variations: Costs can fluctuate based on geographic location, impacting both material and labor costs.
- Permitting and Regulations: Depending on local laws, obtaining permits can incur additional expenses.
The combination of these factors creates a comprehensive picture of what to expect when embarking on a deck-building project.
Final Thoughts on Deck Construction Budgeting
Budgeting for a deck construction project requires careful consideration. A clear understanding of material costs, labor pricing, and potential ROI can lead to more informed decisions.
It is advisable to conduct thorough research before initiating construction. Getting multiple quotes, exploring different materials, and assessing personal preferences are essential steps.
In summary, setting a realistic budget can help manage expectations and avoid unexpected financial burdens during the construction process. This article serves as a practical guide to navigate through the complexities of deck construction costs.